SBS Ecoclean Group Blog
A hub for insights, updates, and deep dives into the world of industrial parts cleaning and surface processing, with solutions for Precision Technologies, HealthCare, Mobility, Environment and Renewable Energy.
Your go-to resource for the latest trends, technologies and best practices with: Industry Insights, Sustainability Focus, Expert Opinions, Company Updates and Technical Guides.
A Clear Focus on Cleaning Effectiveness
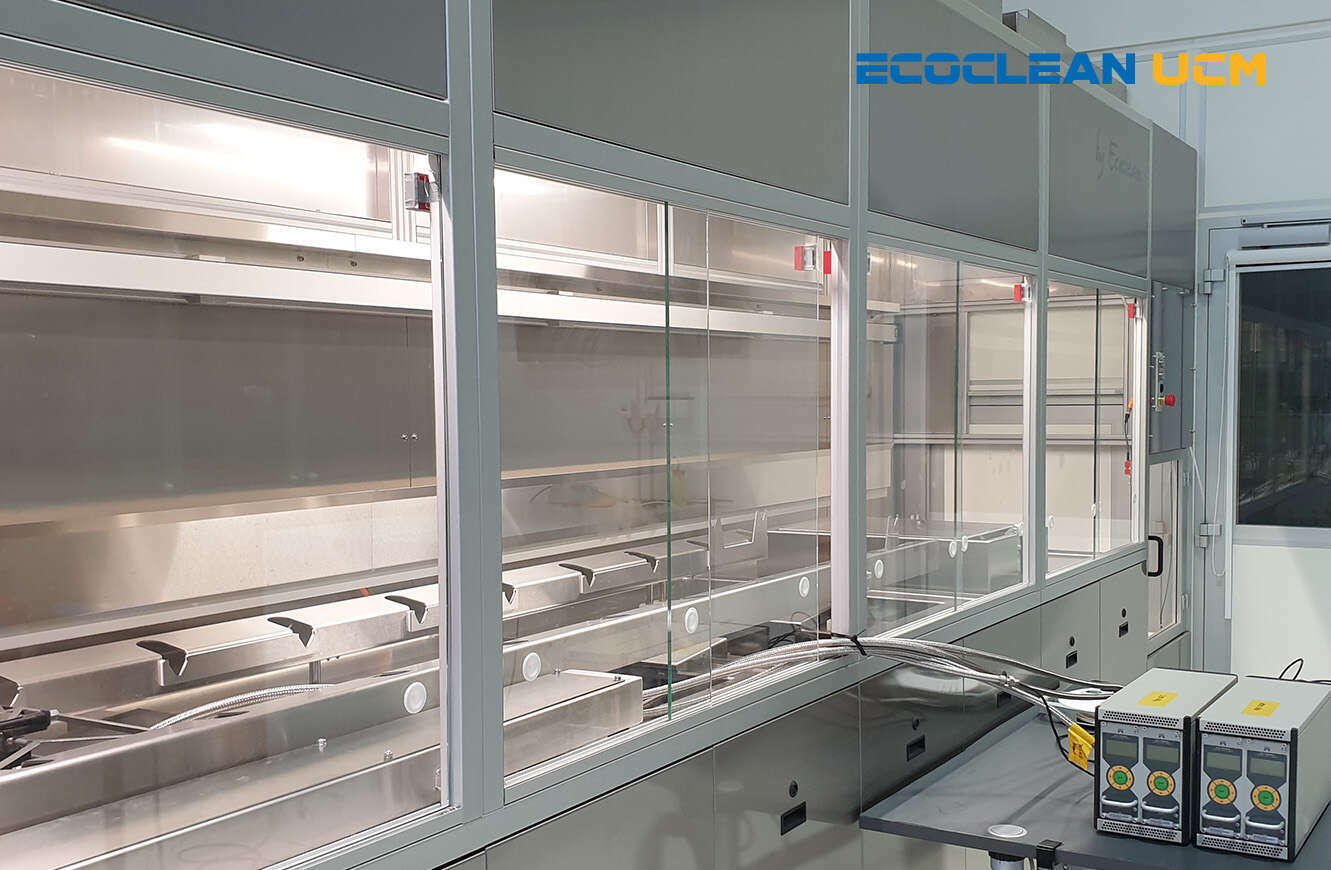
Our innovative APM solution has taken a major step forward: it’s now even more powerful in monitoring the frequency and power of high-frequency ultrasound — without any contact with the parts being cleaned. This makes it especially valuable for industries where ultra-fine cleanliness of highly sensitive components is critical.
An Award as a background
It all began at the end of 2022, when Ecoclean was honored with the FiT2Clean Award at parts2clean for our breakthrough Acoustic Performance Measurement (APM) technology. At that time, we had just launched the system: a specialized microphone capable of monitoring ultrasonic cleaning performance, frequency, and temperature during the cleaning process. This innovation allowed deviations to be detected and documented in real time.
What made the solution award-worthy? APM technology enables process adjustments while sensitive parts are still in the ultrasonic bath. Rather than waiting for the cleaning cycle to end and reviewing the results afterward, operators can intervene during the process itself— ensuring optimal results without delay.
From Innovation to Implementation: Service, support, and training.
Since the launch, our service team has been actively supporting customers in bringing APM technology into daily operation. We know that complex technologies require more than just installation — they demand the right know-how. That’s why we provide in-depth training for machine operators to ensure they can fully leverage the benefits of APM.
To maintain accuracy and reliability over time, we also offer professional system calibration services —to ensure consistent performance with precise measurement.
Now: wider range of cleaning applications
We’ve taken APM to the next level. The technology has been further developed to offer even greater precision in monitoring the frequency and power of high-frequency ultrasound. This enhancement now supports both open multi-stage immersion systems and closed chamber cleaning systems, expanding its usability across a wide range of cleaning procedures.
Through a series of tests, we’ve proven that even sound waves in the high-frequency range—up to two megahertz—can be reliably detected using laser-acoustic microphones. These findings were the foundation for expanding our APM solution, unlocking new levels of control and insight for our customers’ most demanding cleaning processes.
Proving the Precision: How We Validated the Extended Frequency Range
To verify the reliable detection of the frequency spectrum, we conducted a comprehensive series of tests using a laser-acoustic microphone during the development of our enhanced APM measurement system. These tests were carried out on our UCMSmartLine ultrasonic multi-stage immersion cleaning system, as well as on systems equipped with 500 kHz and 1,000 kHz plate transducers.
Additionally, we included plate transducers with oscillation frequencies of 40, 80, and 120 kHz —already integrated into the system, to compare performance with our earlier APM technology, which used condenser microphones.
The results confirmed that the signal-to-noise ratio across the entire frequency band is sufficiently high to detect ultrasonic waves up to 2 MHz. We also identified the optimal distance from the bath surface at which the laser-acoustic microphone must be positioned. Despite increasing attenuation of sound waves in air at higher frequencies, the ideal distance turned out to be comparable to that of the condenser microphones previously used for low-frequency measurements, making the transition seamless for existing setups.
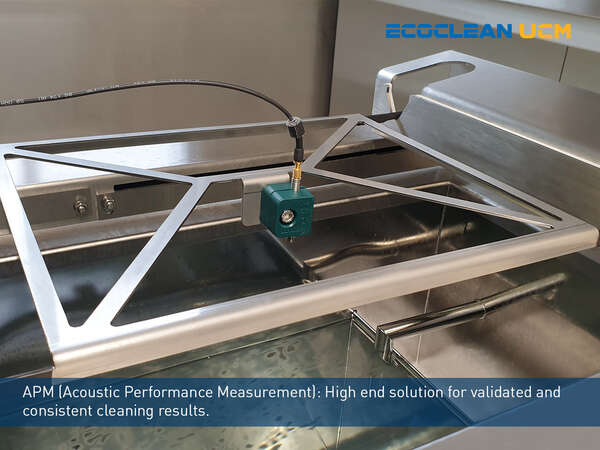
High end solution for validated and consistent cleaning results: Like in this example picture, the microphone is installed on US station, not immersed in the medium.
The Benefits of Contactless and Motionless Measurement
Unlike hydrophones, our APM solution performs measurements without direct contact and without any movement, offering a range of advantages. It can be used safely in environments with aggressive chemicals, without contaminating the cleaning media or putting the measuring equipment at risk. And because the measurement is motionless, it’s both reproducible and fully inline — ideal for consistent process monitoring.
Another key advantage: APM technology can also be applied in closed cleaning and rinsing tanks, such as those used for PPC (Pulsated Pressure Cleaning) application and chamber cleaning systems. The system can detect ultrasonic frequency and sound pressure even through “walls”.
By the way… PPC is a technology developed by Ecoclean, with patent applied, what underscores our commitment to driving innovation in advanced cleaning solutions.
For quick and easy on-site verification, we also offer handheld calibrators to test both the laser-acoustic and condenser microphones used in the system.
Interested in learning more about Acoustic Performance Measurement (APM) technology?
We’re here to help! Whether you’re looking to integrate APM into your systems, need a demo, or simply want more details—feel free to reach out:
E-Mail: service.monschau@ecoclean-group.net, Phone: +49 (0) 2472 83-501
Examine and improve processes | on site with customers
In parts cleaning, we not only look at the process in which our system is used, but also at what influences the cleanliness to be achieved. We look for disruptive factors that can introduce contamination that no one has yet noticed. We look at what happens to the parts after cleaning, how they are further processed and what contamination risks arise. We advise on how cleaning processes can be adapted or even changed. And we work together with the employees on site at our customers' production facilities to ensure that the adjustments are implemented, and a culture is created around the topic of avoiding further sources of contamination.
Process analysis is one of the consulting services offered by the Ecoclean Academy. Among other things, upstream and downstream processes are scrutinized.
BUT it's not just about the analysis described above - it's also about optimization. For issues such as increased cleaning requirements due to additional quantities of parts - or new parts with different requirements - the Ecoclean Academy helps customers to analyze whether they can solve the new tasks with an existing system and what else is required.
At a glance:
- Upstream and downstream processes are scrutinized;
- Existing processes are analyzed and sources of disruption identified;
- Recommendations are made and implemented together with the customer;
- The workforce is made aware of the influence of the entire production chain on the cleaning result.
- Changes to the original requirements, such as higher throughput or new parts, are analyzed and suggestions for optimization are made.
Our services are tailored to the needs of our customers. The duration and costs depend on the scope of the services.
Contact
Are you ready for specific recommendations? Contact us to arrange a visit: academy.filderstadt(at)ecoclean-group.net
More information
More information here.
Challenge accepted: Maximum cleanliness, shortest cycle times, fragile components.
We take the example of bipolar plates and ask our expert from the Ecoclean Center of Competence in Monschau, Germany, Joachim Ritter:
Why is this a special topic for industrial parts cleaning?
Bipolar plates consist of 2 layers (cathode and anode), usually made of uncoated stainless-steel alloys or coated stainless steel carriers, which are extremely thin and very sensitive. The raw material for manufacturing metal bipolar plates is usually unwound from a coil. This means that impurities of an unknown nature may already be present on the raw material. The material for the plates is formed, cut, and stamped using special oils.
In addition to filmic contamination, these processes also generate particulate contamination such as flake burrs, cutting chips, fibers and general contaminants from the air.
The requirements for cleanliness are very high, as any particle that is not removed can later cause a problem in the functional process.
In addition, such plates are manufactured at very high production speeds - the cycle time per part plays a very important role. Part cleaning solutions must be optimally integrated into this process.
How important it is to know the exact origin of the contaminants we want to remove?
To answer this question, we need to look at one of the most important steps in the production of bipolar plates: In a process known as "joining," the anode and cathode plates are placed on top of each other and typically welded together by laser. The welding process can be a source of contamination, which can adversely affect the subsequent performance of the fuel cell.
As can be seen in the picture above, one of the possible contaminants that can appear on such a bipolar plate are sootmarks.
These are usually caused by residual organic matter or oil particles on the surface that burn off during the welding process.
We at Ecoclean go back a few steps in the production cycle and take a close look at all the process steps.
We do this because it is important to know in advance what kind of contaminants are involved.
With our experience, we can advise our customers at this stage to use oils that can be removed later without leaving any residue.
Our solutions are therefore not just about parts cleaning, but also about improving production processes.
What else can we get clean with the industrial parts cleaning technology developed for bipolar plates?
With our technology, we can clean not only flat bipolar plates, but also cubic components such as electronic components or housings, i.e. various metallic materials with high cleanliness requirements and short cycle times.
This also includes components such as battery cell cups, heat sinks or battery connectors.
The cleaning of small parts, pre-punched as an endless belt, can also be cleaned in one piece.
Every particle that is not removed can cause problems later. Therefore, cleaning requirements are very high and require experience and expertise.
Let's take a look at how Ecoclean can support the manufacturing process, using the production of bipolar plates as an example:
For example, bipolar plates for automotive fuel cells are made from pressed graphite powder or stainless steel alloys.
The surfaces of these workpieces are usually contaminated with various substances and elements generated during the manufacturing process.
We have a lot of experience in this area - the following production steps involve forming and cutting the coil material. Oils and emulsions used in these processes can also contaminate the plates.
As mentioned earlier, oxides and sootmarks can also occur later when the plates are joined.
It is extremely important to clean the plates before subsequent processes such as coating, etc. We are able to guarantee the required particulate purity, degreasing and removal of contaminants.
This is the only way to ensure that a dense and perfectly coated bipolar plate is later used in the fuel cell and that the maximum power yield is achieved. We are active in final cleaning, surface preparation and treatment. Here we offer very efficient solutions.
What cleaning processes are applied?
There are several cleaning processes on the market. Each manufacturer must carefully weigh the pros and cons before making a decision.
For example, one solution on the market is CO2 blasting. However, we view this very critically because the bipolar plates are typically used in PEM (proton-exchange membrane) fuel cells to minimize CO2 emissions.
The use of CO2 blasting as a cleaning process is possible, but in our opinion contradictory when you are producing something that should be a more environmentally friendly solution.
Also, the high consumption of CO2 gas and compressed air is a cost factor that needs to be evaluated before a decision is taken. We see this process as more of a partial solution, good for selectively removing traces of smoke on a manageable scale. We do not recommend relying on it for the entire cleaning process.
Other solutions that manufacturers can use either individually or in combination.
We have obtained very good results in cleaning bipolar plates with steam, i.e. hot air processes. It is a fast process that is very effective, especially in removing stains and substances, while using very little liquid. When used correctly, this process allows the oil to evaporate without leaving any residue. The right temperature curves are crucial here.
Depending on the surface, we have also achieved good results with our hydro-cleaning process. We use nozzles that release the medium at a certain pressure and temperature.
To complement the cleaning process, we use other technologies such as ultrasonic cleaning, pressure-cycling rinsing or plasma cleaning, depending on the level of contamination and requirements.
In addition to water- or solvent-based chamber systems such as the EcoCwave or EcoCcore or one of the ultrasonic in-line immersion systems from UCM AG, we now offer the GEN-2 series EcoCbelt as a system for cleaning bipolar plates.
This is a continuous cleaning system in which all possible process variants such as spray cleaning, steam cleaning, plasma cleaning, hydro cleaning, CO2 blasting and drying can be implemented as required in the system concept.
The transport system is designed for sensitive components such as electronic components, bipolar plates, etc.
Is it possible to test component, contamination, and the production requirements in advance?
At our Center of Competence in Monschau, Germany, we are able to perform tests on originally contaminated components under very close to production conditions. Our laboratories are equipped with test methods such as surface tension, fluorescence analysis and infrared spectroscopy. Not only the cleaning processes but also the cycle times are tested in our facilities.
Contact
Phone: +49 2472 83-0
Email: sales.monschau(at)ecoclean-group.net
Medical Device Manufacturing - Cleaning, Passivation and Final Packaging Solutions for the Medical Device Industry
Fabio Cordaro takes us on a deep dive into the most relevant topics in medical device manufacturing.
Why is the cleaning of implants prior to coating a critical step in the manufacturing process?
Prior to coating, implants must be thoroughly cleaned of any contaminants such as oils, greases, machining fluid residues, or particles that can interfere with coating adhesion and lead to uneven coatings. And improving surface adhesion also plays an important role in durability. Effective cleaning helps to create a clean and uniform surface to which the coating can better adhere. This is essential for the long-term stability and functionality of the implant..
Thorough cleaning eliminates potential sources of contamination that may occur during the manufacturing process This is especially important to ensure implant sterility and prevent patient infection.
What about compliance with regulations and standards?
When it comes to "cleaning, passivation and final packaging," medical device manufacturers need to focus on the FDA (Food and Drug Administration) in America or the MDR (Medical Device Regulation) in the EU, depending on the country. Here are some of the reasons compliance is so important to the medical device industry:
- Proper parts cleaning procedures, passivation processes, and sterile packaging are critical to avoid contamination and ensure product integrity throughout its lifecycle - protecting patient health. These regulations ensure high quality standards in the manufacturing process.
- Regulations require the documentation and traceability of materials and processes used in the manufacture of medical devices. This helps manufacturers to identify problems that may occur during the manufacturing process. In other words, always know exactly what, where and when.
- Compliance with FDA and MDR regulations is often a prerequisite for market access, not only in the United States and the European Union, but also in many other countries around the world. As MedTech manufacturers go global, they must comply with these regulations and need a supplier that can help them navigate the regulatory landscape, rather than just selling equipment detached from the overall process.
Ecoclean has developed a passivation process called Pulsated Pressure Passivation (PPP) to meet the specific needs of the medical industry. How does it work and what are the benefits for MedTech manufacturers?
As far as parts cleaning is concerned, we already work with a process called PPC (Pulsated Pressure Cleaning), which consists of reducing and increasing the pressure in the process chamber filled with the cleaning medium to reach the areas to be cleaned or rinsed, taking advantage of the air contraction once the chamber is ventilated. We have used our experience in this process to offer a technology for the passivation process that we call PPP (Pulsated Pressure Passivation), which allows the surface to be treated with a protective layer regardless of the geometry of the component, since this change in pressure inside the process chamber causes the passivation to chemically flow into all the cavities and holes.
The new passivation process from SBS Ecoclean Group is a quantum leap for medical and high-end technologies.
Traditional atmospheric methods only clean and passivate the external geometry of the parts.
With the new process we are able to clean and passivate implants and instruments even in capillaries, internal geometries and blind holes.
We would be happy to invite you to our application laboratory to demonstrate this groundbreaking process.
PPC and PPP are exclusive cleaning and passivation processes developed by Ecoclean!
We have a MedTech Test Center at our Ecoclean Center of Competence in Monschau, Germany. What do we offer there?
Ecoclean has a fully equipped Technology Center in Monschau, Germany, with a cleanroom laboratory and a validated cleanroom for system and process design. This facility allows us to precisely develop customized solutions for various medical device applications. In addition, our solutions can be easily duplicated for implementation across multiple manufacturing sites.
The MedTech Test Center offers a range of solutions for cleaning and packaging medical implants and instruments. Manufacturers will find our complete portfolio, from single-chamber solvent and water-based systems to multi-stage ultrasonic cleaning machines. With this infrastructure, we can evaluate the best process for MedTech needs. It is important to remember that one of the biggest challenges for manufacturers in the medical device component industry is keeping up with the ever-changing regulatory environment. This is where the SBS Ecoclean Group comes in, offering not only the technology of our systems for parts cleaning, passivation and sterile packaging, but also qualified support to meet the requirements and a recalibration service to bring production up to date. And, of course, always in compliance with the latest MDR and FDA regulations.
Which Ecoclean parts cleaning system for the MedTech industry combines innovative technology, sustainability and precision?
The SBS Ecoclean Group brands Ecoclean and UCM AG are collaborating on advanced cleaning systems for medical devices, particularly in the field of endoscopy. The result of this collaboration is the UCMPerformanceLine, an ultrasonic multi-chamber immersion cleaning system designed to maintain the high standards of cleanliness required for optical lens systems in medical endoscopes. The UCMPerformanceLine is engineered to efficiently and accurately clean small, delicate parts such as coated lens systems, ensuring they meet stringent cleanliness specifications. The system features a modular design for customized cleaning processes, automated part transport, and is directly connected to a cleanroom.
What else do we have in our portfolio of medical component cleaning systems?
We combine Ecoclean and UCM AG technologies to provide solutions from A to Z, depending on customer requirements and after conducting trials at our test centers around the world. For pre-cleaning of MedTech parts and components, we have aqueous or solvent-based chamber systems such as the EcoCwave or the EcoCore. For parts cleaning after finishing, we offer UCM inline immersion systems and finally for final cleaning and/or passivation we offer among others the UCM PerformanceLine. For very small and complex parts we have for example the UCMIndexLine - in summary: we have the right system for the required application.
What technologies distinguish Ecoclean's MedTech solutions?
Ecoclean differentiates itself through the use of specialized medical device software, RFID technology, and meticulous audit trails. These technologies ensure that all component identification, documentation and traceability requirements are not only met, but exceeded.
Our team of experts is dedicated to providing comprehensive support throughout the qualification process, including IQ (Installation Qualification), OQ (Operational Qualification), and PQ (Performance Qualification) upon request. We understand the importance of compliance and are committed to guiding our customers every step of the way.
Contact
Phone: +49 (0)2472 83-0
Email: testcenter.monschau(at)ecoclean-group.net