SBS Ecoclean Group Blog
Informationen, Updates und detaillierte Einblicke in die Welt der industriellen Teilereinigung und Oberflächenbearbeitung mit Lösungen für Präzisionstechnologien, Gesundheitswesen, Mobilität, Umwelt und erneuerbare Energien.
Die Quelle für die neuesten Trends, Technologien und Best Practices: Einblicke in die Branche, Fokus auf Nachhaltigkeit, Expertenmeinungen, Neuigkeiten aus der Industrie und technische Tipps.
Ein klarer Fokus auf Effizienz
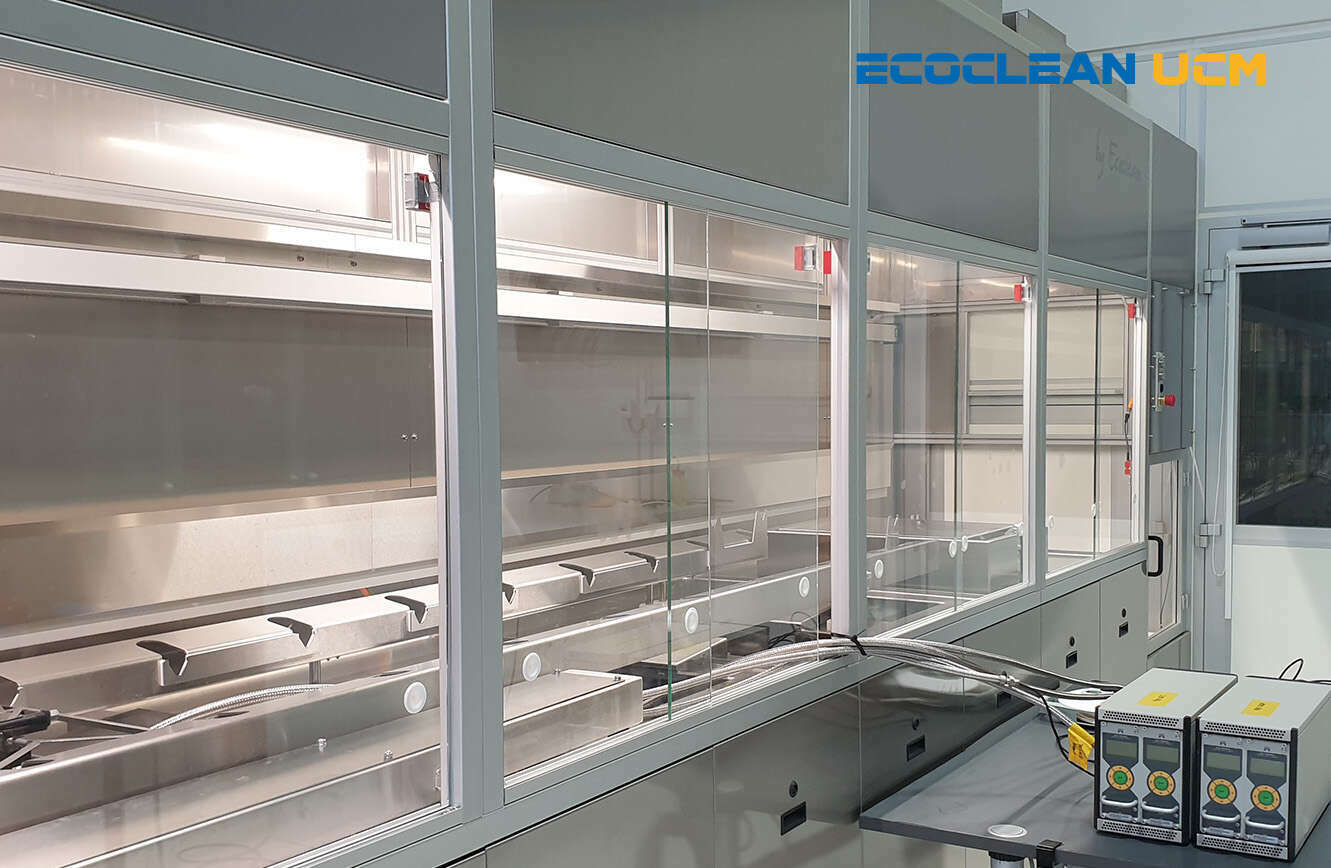
Unsere innovative APM-Lösung hat einen wichtigen Schritt vorwärts gemacht: Sie ist jetzt noch leistungsfähiger bei der Überwachung der Frequenz und Leistung von Hochfrequenz-Ultraschall - ohne jeglichen Kontakt mit den zu reinigenden Teilen. Das macht sie besonders wertvoll für Branchen, in denen die Sauberkeit hochempfindlicher Komponenten entscheidend ist.
Eine Auszeichnung als Hintergrund
Alles begann Ende 2022, als Ecoclean auf der parts2clean mit dem FiT2Clean Award für unsere bahnbrechende Acoustic Performance Measurement (APM) Technologie ausgezeichnet wurde. Zu diesem Zeitpunkt hatten wir das System gerade erst auf den Markt gebracht: ein spezielles Mikrofon, das in der Lage ist, die Ultraschall-Reinigungsleistung, die Frequenz und die Temperatur während des Reinigungsprozesses zu überwachen. Mit dieser Innovation konnten Abweichungen in Echtzeit erkannt und dokumentiert werden.
Was machte die Lösung preiswürdig? Die APM-Technologie ermöglicht Prozessanpassungen, während sich die empfindlichen Teile noch im Ultraschallbad befinden. Anstatt auf das Ende des Reinigungszyklus zu warten und die Ergebnisse danach zu überprüfen, können Anwender bereits während des Prozesses eingreifen und so ohne Verzögerung optimale Ergebnisse erzielen.
Von der Innovation zur Umsetzung: Service, Unterstützung und Schulung.
Seit der Markteinführung unterstützt unser Serviceteam Kunden aktiv dabei, die APM-Technologie in den täglichen Betrieb zu bringen. Wir wissen, dass komplexe Technologien mehr als nur die Installation erfordern - sie verlangen auch das richtige Know-how. Deshalb schulen wir das Personal an den Maschinen gründlich, damit es die Vorteile von APM voll ausschöpfen kann.
Um die Genauigkeit und Zuverlässigkeit im Laufe der Zeit aufrechtzuerhalten, bieten wir auch professionelle Systemkalibrierungsdienste an, um eine gleichbleibende Leistung mit präzisen Messungen zu gewährleisten.
Heute: breiteres Spektrum an Reinigungsanwendungen
Wir haben APM auf die nächste Stufe gebracht. Die Technologie wurde weiterentwickelt, um eine noch höhere Präzision bei der Überwachung der Frequenz und Leistung von Hochfrequenz-Ultraschall zu bieten. Diese Verbesserung unterstützt nun sowohl offene mehrstufige Tauchsysteme als auch geschlossene Kammerreinigungssysteme und erweitert die Verwendbarkeit für eine breite Palette von Reinigungsverfahren.
In einer Reihe von Tests haben wir nachgewiesen, dass auch Schallwellen im Hochfrequenzbereich - bis zu zwei Megahertz - mit laser-akustischen Mikrofonen zuverlässig erfasst werden können. Diese Erkenntnisse waren die Grundlage für die Erweiterung unserer APM-Lösung, die unseren Kunden neue Möglichkeiten der Kontrolle und des Einblicks in ihre anspruchsvollen Reinigungsprozesse eröffnet.
Nachweis der Präzision: Wie wir den erweiterten Frequenzbereich validiert haben
Um die zuverlässige Erfassung des Frequenzspektrums zu verifizieren, haben wir während der Entwicklung unseres verbesserten APM-Messsystems eine umfassende Testreihe mit einem laserakustischen Mikrofon durchgeführt. Diese Tests wurden an unserer UCMSmartLine (Ultraschall-Reihentauchanlage) sowie an Systemen durchgeführt, die mit 500-kHz- und 1.000-kHz-Plattenschwingern ausgestattet sind.
Zusätzlich haben wir Plattenwandler mit Schwingungsfrequenzen von 40, 80 und 120 kHz in das System integriert, um die Leistung mit unserer früheren APM-Technologie zu vergleichen, bei der Kondensatormikrofone verwendet wurden.
Die Ergebnisse bestätigten, dass das Verhältnis von Signal zu Rauschen über das gesamte Frequenzband ausreichend hoch ist, um Ultraschallwellen bis zu 2 MHz zu erkennen. Wir ermittelten auch den optimalen Abstand zur Badoberfläche, in dem das laserakustische Mikrofon positioniert werden muss. Trotz der zunehmenden Dämpfung der Schallwellen in der Luft bei höheren Frequenzen erwies sich der ideale Abstand als vergleichbar mit dem von Kondensatormikrofonen, die bisher für niederfrequente Messungen verwendet wurden, so dass ein nahtloser Übergang zu den bestehenden Aufbauten möglich ist.
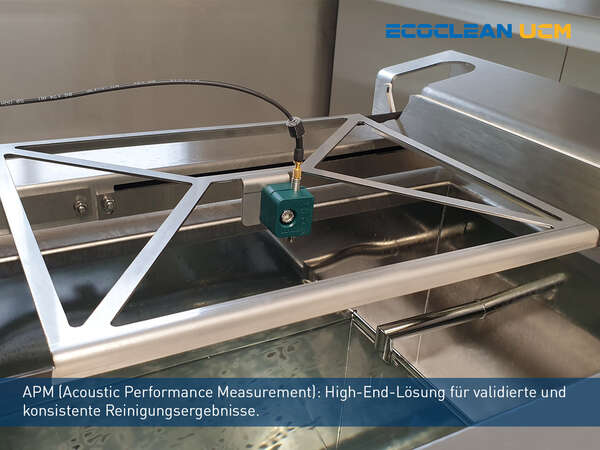
High-End-Lösung für validierte und konsistente Reinigungsergebnisse: Wie in diesem Beispielbild ist das Mikrofon auf der US-Station installiert und nicht in das Medium eingetaucht.
Die Vorteile einer berührungs- und bewegungslosen Messung
Im Gegensatz zu Hydrophonen führt unsere APM-Lösung Messungen ohne direkten Kontakt und ohne jede Bewegung durch, was eine Reihe von Vorteilen bietet. Sie kann sicher in Umgebungen mit aggressiven Chemikalien eingesetzt werden, ohne die Reinigungsmedien zu verunreinigen oder die Messgeräte zu gefährden. Und da die Messung ohne Bewegung erfolgt, ist sie sowohl reproduzierbar als auch vollständig inline - ideal für eine konsistente Prozessüberwachung.
Ein weiterer entscheidender Vorteil: Die APM-Technologie kann auch in geschlossenen Reinigungs- und Spültanks eingesetzt werden, wie sie für PPC-Anwendungen (Pulsated Pressure Cleaning) und Kammerreinigungssysteme verwendet werden. Das System kann Ultraschallfrequenz und Schalldruck sogar durch "Wände" hindurch erfassen.
Übrigens... PPC ist eine von Ecoclean entwickelte und zum Patent angemeldete Technologie, die unser Engagement unterstreicht, Innovationen bei fortschrittlichen Reinigungslösungen voranzutreiben.
Für eine schnelle und einfache Überprüfung vor Ort bieten wir auch tragbare Kalibratoren an, mit denen sowohl die laserakustischen als auch die im System verwendeten Kondensatormikrofone getestet werden können.
Möchten Sie mehr über die Acoustic Performance Measurement (APM) Technologie erfahren?
Wir sind für Sie da! Ganz gleich, ob Sie APM in Ihre Systeme integrieren möchten, eine Vorführung benötigen oder einfach nur weitere Details erfahren möchten - Sie können sich gerne an uns wenden:
E-Mail: service.monschau@ecoclean-group.net, Phone: +49 (0) 2472 83-501
Prozesse untersuchen und verbessern | bei Kunden vor Ort
In der Teilereinigung schauen wir nicht nur auf den Prozess, in dem unser System eingesetzt wird, sondern auch auf das, was die zu erreichende Sauberkeit beeinflusst. Wir suchen nach Störfaktoren, durch die Verunreinigungen eingeschleppt werden können, die noch niemand bemerkt hat. Wir schauen, was mit den Teilen nach der Reinigung passiert, wie sie weiterverarbeitet werden und welche Kontaminationsrisiken dabei entstehen. Wir beraten, wie Reinigungsprozesse angepasst oder sogar geändert werden können. Und wir arbeiten mit der Belegschaft vor Ort in den Produktionsstätten unserer Kunden zusammen, damit die Anpassungen umgesetzt werden und eine Kultur rund um das Thema Vermeidung weiterer Kontaminationsquellen entsteht.
Prozessanalyse gehört zu den Beratungsleistungen der Ecoclean Academy. Hier werden unter anderem vor- und nachgelagerte Prozesse unter die Lupe genommen.
ABER es bleibt nicht bei der oben beschriebenen Analyse - es geht auch um Optimierung. Bei Themen wie erhöhter Reinigungsbedarf durch zusätzliche Teilemengen - oder neue Teile mit unterschiedlichen Anforderungen - hilft die Ecoclean Academy den Kunden bei der Frage, ob sie die neuen Aufgaben mit einer bestehenden Anlage lösen können und was sonst noch dafür notwendig ist.
Auf einen Blick:
- Vor- und nachgelagerte Prozesse werden unter die Lupe genommen;
- Bestehende Prozesse werden analysiert und Störquellen identifiziert;
- Empfehlungen werden ausgesprochen und gemeinsam mit dem Kunden umgesetzt;
- Die Belegschaft wird über den Einfluss der gesamten Produktionskette auf das Reinigungsergebnis sensibilisiert.
- Änderungen der ursprünglichen Anforderungen wie z. Bsp., höherer Durchsatz oder neue Teile werden analysiert und Vorschläge zur Optimierung werden unterbreitet.
Unsere Dienstleistungen sind auf die Bedürfnisse unserer Kunden zugeschnitten. Dauer und Kosten richten sich nach dem Umfang der Dienstleistungen.
Kontakt
Sind Sie bereit für konkrete Empfehlungen? Kontaktieren Sie uns, um einen Besuch zu vereinbaren: academy.filderstadt(at)ecoclean-group.net
Mehr Informationen
Weitere Informationen hier.
Unser Global Newsletter EcoCnews Winter 2024 ist JETZT online!
Globaler Anbieter lokaler Lösungen: Ecoclean führt den Wandel an
Die SBS Ecoclean Group passt sich an und entwickelt sich weiter, um den globalen Herausforderungen von heute gerecht zu werden. Denn was unsere Kunden brauchen, ist ein vertrauenswürdiger Partner, eine globale Gruppe mit lokaler Expertise, die ihre spezifischen Bedürfnisse erfüllt – nicht nur in Bezug auf die Suche nach dem richtigen System für ihre Teilereinigungs- und Oberflächenverarbeitung, sondern auch durch einen beratenden Ansatz, der echte Innovation, umfassende Dienstleistungen und Know-how bietet.
Die Welt verändert sich in rasantem Tempo, angetrieben von Megatrends wie Automatisierung, Nachhaltigkeit und Sicherheit, die sowohl von unseren Kunden als auch von uns Anpassungen verlangen. Als einer der führenden Anbieter für industrielle Teilereinigung stellt sich die SBS Ecoclean Group diesen Herausforderungen mit einem proaktiven und zukunftsorientierten Diversifizierungsansatz. Wir tun dies, indem wir unsere Kompetenzen und Ressourcen kreativ kombinieren, um völlig neue Systeme zu entwickeln, die neue Standards und Bedürfnisse optimal erfüllen. So bieten wir Lösungen an, nicht nur Produkte. Um mit den anspruchsvollen Anforderungen des Marktes Schritt zu halten, haben wir unser Portfolio weiter ausgebaut und spezielle Lösungen für Hightech-Branchen wie Medizintechnik und High Purity und für die neuen Herausforderungen in der Luft- und Raumfahrt und Mobilität entwickelt. Wir haben auch bedeutende Fortschritte im Bereich grüner Wasserstoff erzielt, indem wir die Serienproduktion unserer dezentralen Elektrolyseursysteme – EcoLyzer – aufgenommen haben.
Unsere weltweiten Standorte und lokalen Partnerschaften ermöglichen es uns, gezielt auf regionale Bedürfnisse einzugehen und unsere Position in wichtigen Märkten weiter auszubauen. Gleichzeitig greifen wir auf eine globale Infrastruktur von Ressourcen, Dienstleistungen und Know-how zurück. Im Jahr 2024 expandierten wir auch an mehrere Standorte, wodurch wir in der Lage sind, Lösungen vor Ort zu entwickeln und sie an die lokalen Bedürfnisse anzupassen. So starten wir in das neue Jahr 2025 noch gestärkter als „globaler Anbieter lokaler Lösungen“ für unsere Kunden.
Mehr dazu in der Winterausgabe 2024/2025 unseres Newsletters.
Im Artikel „Next-level industrial cleaning“ stellen wir modulare Lösungen für maßgeschneiderte hochreine Reinigungsaufgaben vor. In Bezug auf aktuelle Innovationen werden in diesem Artikel Präzisionsreinigungslösungen für die Medizintechnik- und Uhrenindustrie vorgestellt, wie z. B. das bahnbrechende PPP-Verfahren (Pulsed Pressure Passivation). Intelligente Technologien für eine nachhaltige industrielle Reinigung, wie Smart Drying, Acoustic Performance Measurement (APM) und unsere Lab-on-a-Chip-Technologie, ermöglichen einen umweltfreundlichen Ansatz in Kombination mit Effizienz.
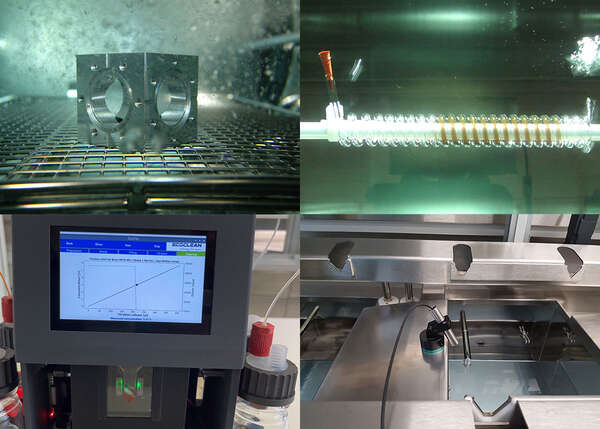
Pulsed Pressure Cleaning (PPC), Pulsed Pressure Passivation (PPP), lab-on-a-chip Technologie und Acoustic Performance Measurement (APM).
In dem Artikel „Stärkung unserer globalen Präsenz durch lokale Expertise“ zeigen wir, wie wichtig es ist, ein regionaler Experte zu werden, um umfassende Lösungen und Dienstleistungen anzubieten, die auf die lokalen Märkte abgestimmt sind und den lokalen Kundenbedürfnissen entsprechen. Dazu gehören die strategische Partnerschaft mit JKS Engineering (M) Sdn Bhd in Malaysia und die Erweiterung unserer tschechischen Tochtergesellschaft, um neben der Herstellung unserer automatisierten Fördersysteme auch die lokale Produktion einer völlig neuen EcoCcompact-Produktfamilie zu ermöglichen. Ein weiteres Highlight: ein exklusives Verkaufsteam, das die iberische Region abdeckt, um die Bedürfnisse unserer Kunden in Spanien und Portugal noch besser zu erfüllen.
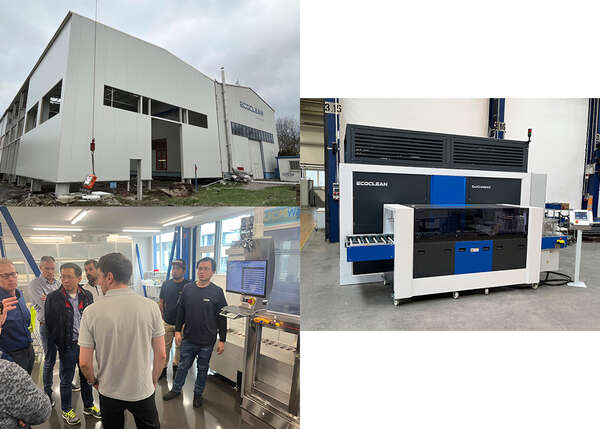
Beispiele für lokale Bemühungen: Erweiterung unserer tschechischen Tochtergesellschaft und strategische Partnerschaft mit JKS Engineering in Malaysia.
In dem Artikel „Pionierarbeit für eine grüne Wasserstoffzukunft“ stellen wir die Geschichte unseres eigenen Elektrolyseurs vor und erklären, wie unser Diversifizierungsansatz uns zur Entwicklung des EcoLyzers geführt hat. Heute versorgt Ecoclean Kunden weltweit mit grünem Wasserstoff als nachhaltige Energiequelle und deckt so die steigende Nachfrage nach sauberer Energie. Das skalierbare, wartungsarme alkalische Elektrolysesystem bietet Wasserstofflösungen für eine Reihe von Anwendungen. Mit dem EcoLyzer helfen wir der Industrie, von fossilen Brennstoffen auf eine grünere Zukunft umzusteigen.
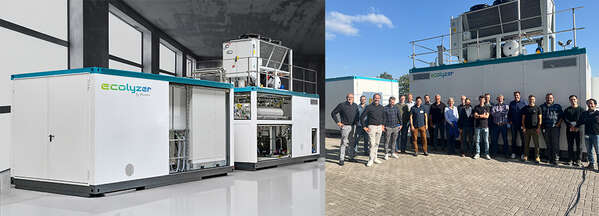
Das EcoLyzer-Team präsentiert stolz den Elektrolyseur P200, der 2024 in Serieproduktion ging.
Im Artikel „Ecoclean in den USA: Weitere Schritte in der Medizintechnik und -systeme“ zeigen wir, wie Ecoclean sein Engagement in der US-amerikanischen Medizintechnikindustrie durch verstärkte Partnerschaften und ein erweitertes Produktangebot weiter ausbaut. Durch eine Partnerschaft mit EnPak in Warsaw, Indiana, haben wir den Grundstein für das „MedTech Clean&Pack Solutions by Ecoclean and EnPak“ gelegt, ein hochmodernes MedTech-Reinigungslösungszentrum, das lokale Lösungen für Vorreinigung, Endreinigung und Reinigungsdienstleistungen anbietet – das von EnPak für Verpackung, Inspektion, Bestandsverwaltung, Auftragsabwicklung und Validierung unterstützt wird. Darüber hinaus wird unsere EcoCcompact-Produktfamilie erweitert, um dem Bedarf an hochwertigen, kostengünstigen Lösungen gerecht zu werden, die den sich wandelnden Anforderungen der lokalen Industrie entsprechen.
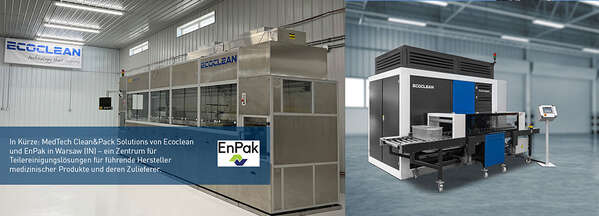
Schlüsselfertige Lösungen von Ecoclean für die US-amerikanische Medizintechnikindustrie mit EnPak an unserer Seite & die neue EcoCcompact-Produktfamilie stellt sich vor.
Die Herausforderung: Höchste Sauberkeit, kürzeste Taktzeiten, fragile Bauteile.
Wir nehmen die Bipolarplatten als Beispiel und fragen unseren Experten, was er uns darüber erzählen kann:
Warum ist dies ein spezielles Thema für die industrielle Teilereinigung?
Bipolarplatten bestehen aus 2 Folien (Kathode und Anode), meistens aus unbeschichteten Edelstahllegierungen oder beschichteten Edelstahlträgern, die extrem dünn und sehr empfindlich sind. Das Ausgangsmaterial zur Herstellung metallischer Bipolarplatten wird üblicherweise vom Coil abgewickelt. Das bedeutet, dass bereits auf dem Rohmaterial Verunreinigungen unbekannter Art vorhanden sein können.
Das Material für die Platten wird unter Einsatz spezieller Öle umformt, geschnitten und gestanzt.
Bei diesen Prozessen werden neben der filmischen Verschmutzung auch partikuläre Verunreinigungen entstehen, wie z.B: Flittergrate, Schneidspäne sowie Fasern und allgemeiner Schmutz aus der Luft.
Die Anforderungen an die Sauberkeit sind sehr hoch, denn jeder nicht abgereinigte Partikel kann später zu einer Fehlfunktion in der Funktionsprozess führen.
Darüber hinaus erfolgt die Herstellung solcher Platten bei sehr hoher Produktionsgeschwindigkeit - also die Taktzeit pro Teil spielt hier eine sehr wichtige Rolle. Die Lösungen für die Teilereinigung müssen optimal in diesen Prozess integriert werden.
Wie wichtig ist es, die genaue Herkunft der Schadstoffe zu kennen, die wir entfernen wollen?
Um diese Frage zu beantworten, müssen wir einen der wichtigsten Schritte bei der Herstellung von Bipolarplatten betrachten: Beim sogenannten „Fügen“, werden Anoden- und Kathodenplatte übereinandergelegt und in der Regel mittels Laser verschweißt. Bei diesem Schweißprozess können Verunreinigungen entstehen, die die spätere Funktion der Brennstoffzelle negativ beeinträchtigen.
Eine der möglichen Verunreinigungen, die auf einer solchen Bipolarplatte auftreten können, sind Schmauchspuren, wie sie im Bild zu erkennen sind.
Diese entstehen in der Regel durch, auf der Oberfläche befindliche, Restorganik oder Ölanteile, die beim Schweißvorgang verbrennen. Hier gehen wir, von Ecoclean ein paar Schritte zurück, in die Produktion und schauen uns alle Prozessschritte genau an. Das machen wir, weil es wichtig ist, im Vorfeld zu erkennen, um welche Verschmutzungen es sich handelt. Mit unserer Erfahrung können wir unsere Kunden an dieser Stelle gut beraten, damit sie möglichst Öle einsetzen, welche sich später rückstandsfrei entfernen lassen. Unsere Lösungen betreffen somit nicht nur die Reinigung, sondern wir helfen auch dabei Produktionsprozesse zu verbessern.
Was können wir mit der für Bipolarplatten entwickelten industriellen Teilereinigungstechnologie noch sauber bekommen?
Mit unserer Technologie können wir nicht nur flache Bipolarplatten, sondern auch kubische Bauteile wie etwa Elektronikkomponenten oder auch -gehäuse, also diverse metallische Materialien mit hohen Sauberkeitsanforderungen und kurzen Taktzeiten, reinigen. Dazu gehören auch Bauteile wie Batteriezellbecher, Kühlkörper oder etwa Batterieverbinder (Konnektoren).
Auch das Reinigen von Kleinteilen, vorgestanzt als Endlosband, können am Stück gereinigt werden. Jeder nicht abgereinigte Partikel kann später zu Problemen führen. Daher sind die Reinigungsanforderungen sehr hoch und eine entsprechende Erfahrung und Expertise erforderlich.
Schauen wir uns an, wie Ecoclean den Fertigungsprozess unterstützen kann, indem wir die Produktion von Bipolarplatten beispielhaft betrachten:
Bipolarplatten für Automotive-Brennstoffzellen werden beispielsweise aus gepresstem Graphitpulver oder Edelstahllegierungen hergestellt. Die Oberflächen dieser Werkstücke sind in der Regel mit verschiedenen Substanzen und Elementen verunreinigt, die während des Herstellungsprozesses entstehen. Inzwischen haben wir eine Menge Erfahrungen hierzu sammeln können. In den folgenden Produktionsschritten zur Herstellung, wird das Coil-Material geformt und geschnitten. Hier verwendete Ölen und Emulsionen verunreinigen die Platten zusätzlich. Auch wie im letzten Post bereits erwähnt, können später beim Fügen der Platten Oxide und Schmauch entstehen.
Es ist überaus wichtig, die Platten vor den dann folgenden Prozessen, wie dem Beschichten etc., zu reinigen. Wir sind in der Lage die geforderte partikuläre Reinheit, Entfettung und Substanzfreiheit zu garantieren. Nur so wird sichergestellt, dass später eine dichte und perfekt beschichtete Bipolarplatte in der Brennstoffzelle ihren Dienst versieht, und die maximale Leistungsausbeute erreicht wird. Wir sind in der Endreinigung, der Oberflächenvorbereitung und -behandlung aktiv. Wir bieten Ihnen sehr effiziente Lösungen an.
Welche Reinigungsverfahren werden angewandt?
Auf dem Markt werden verschiedene Reinigungsverfahren angeboten. Unter Einbeziehung aller Vor- und Nachteile muss jeder Hersteller seine Entscheidungen sorgsam abwägen.
Eine auf dem Markt vorgestellte Lösungen ist zum Beispiel das CO2-Strahlen. Das sehen wir aber sehr kritisch, weil die Bipolarplatten meistens in PEM-Brennstoffzellen eingesetzt werden, um am Ende die CO2-Emissionen zu minimieren. CO2-Strahlen als Reinigungsverfahren einzusetzen ist möglich, aber aus unserer Sicht widersprüchlich, wenn man eigentlich etwas produziert, dass zu einer sauberen Umwelt beitragen soll. Der mitunter hohe CO2-Gas- und Pressluftverbrauch ist zudem ein Kostenfaktor, der vor einer Entscheidung zu bewerten ist.
Wir sehen dieses Verfahren eher als eine Teillösung, gut um z.B. gezielt Schmauchspuren in überschaubarem Umfang zu entfernen. Wir empfehlen nicht den gesamten Reinigungsprozess davon abhängig zu machen.
Andere Lösungen, die Hersteller entweder einzeln oder in Kombination verwenden können.
Mit Dampf, also Heißluftverfahren, haben wir sehr gute Ergebnisse bei der Reinigung von Bipolarplatten erzielt. Es handelt sich um ein schnelles Verfahren, mit hoher Wirksamkeit insbesondere in Bezug auf Flecken- und Substanzfreiheit bei gleichzeitig geringem Flüssigkeitsverbrauch. Richtig angewandt, lässt dieses Verfahren das Öl rückstandsfrei verdampfen. Hier sind die richtigen Temperaturverläufe entscheidend.
Je nach Oberfläche haben wir auch mit unserem sogenannten Hydro-Cleaning-Verfahren gute Ergebnisse erzielt. Dabei verwenden wir Düsen, die das Medium mit einem bestimmten Druck und einer bestimmten Temperatur abstrahlen.
Zur Ergänzung des Reinigungsprozesses setzen wir je nach Verunreinigung und Anforderung weitere Technologien wie Ultraschallreinigung, Druckwechselspülen oder auch Plasmareinigung ein.
Als System für die Reinigung von Bipolarplatten bieten wir neben wasser- oder lösemittelbasierenden Kammeranlagen wie der EcoCwave bzw. EcoCcore oder einer der Reihentauchanlagen der UCM AG, nun auch EcoCbelt der Baureihe GEN-2 an. Hierbei handelt es sich um eine Durchlaufreinigungsanlage, in der alle möglichen Prozessvarianten wie Spritzreinigen, Dampfreinigen, Plasmareinigen, Hydro-Cleaning, CO2-Strahlen und Trocknung bedarfsgerecht je nach Anforderung im Anlagenkonzept realisiert werden können. Das Transportsystem ist für empfindliche Bauteile, wie Elektronikkomponenten, Bipolarplatten, etc. ausgelegt.
Ist es möglich, Bauteile, Verunreinigungen und die Produktionsanforderungen im Voraus zu testen?
In unserem Kompetenzzentrum in Monschau sind wir in der Lage, Tests mit original verschmutzten Bauteilen sehr produktionsnah durchzuführen. Unsere Labore sind unter anderem mit Prüfverfahren wie Oberflächenspannung, Fluoreszenzanalyse und Infrarotspektroskopie ausgestattet. In unseren Anlagen werden nicht nur die Reinigungsprozesse, sondern auch die Taktzeiten getestet.
Contact
Phone: +49 2472 83-0
Email: sales.monschau(at)ecoclean-group.net
Fertigung in der Medizintechnik - Lösungen für die Reinigung, Passivierung inklusive Reinraum- und Verpackungssystemen.
Fabio Cordaro gewährt uns einen tiefen Einblick in die wichtigsten Themen der Medizinproduktherstellung.
Warum ist die Reinigung von Implantaten vor der Beschichtung ein kritischer Schritt im Herstellungsprozess?
Vor der Beschichtung müssen die Implantate gründlich von Verunreinigungen wie Ölen, Fetten, Rückständen von Bearbeitungsflüssigkeiten oder Partikeln gereinigt werden, die die Haftung beeinträchtigen und zu ungleichmäßigen Beschichtungen führen können. Die Verbesserung der Oberflächenhaftung spielt auch eine wichtige Rolle für die Haltbarkeit. Eine wirksame Reinigung trägt dazu bei, eine saubere und gleichmäßige Oberfläche zu schaffen, auf der die Beschichtung besser haften kann. Dies ist entscheidend für die langfristige Stabilität und Funktionalität des Implantats.
Eine gründliche Teilereinigung beseitigt potenzielle Kontaminationsquellen, die während des Herstellungsprozesses auftreten können. Dies ist besonders wichtig, um die Sterilität des Implantats zu gewährleisten und eine Infektion des Patienten zu verhindern.
Wie sieht es mit der Einhaltung von Vorschriften und Normen aus?
Wenn es um „Reinigung, Passivierung und Endverpackung“ geht, müssen sich Hersteller von medizinischen Geräten nach der FDA (Food and Drug Administration) in Amerika oder der MDR (Medical Device Regulation) in der EU richten, je nach Land. Hier sind einige der Gründe, warum die Einhaltung der Vorschriften für die Medizintechnik so wichtig ist:
- Ordnungsgemäße Verfahren zur Teilereinigung, Passivierung und sterilen Verpackung sind entscheidend, um Verunreinigungen zu vermeiden und die Produktintegrität während des gesamten Lebenszyklus zu gewährleisten - zum Schutz der Gesundheit der Patienten. Diese Vorschriften gewährleisten hohe Qualitätsstandards im Herstellungsprozess.
- Die Vorschriften verlangen die Dokumentation und Rückverfolgbarkeit von Materialien und Prozessen, die bei der Herstellung von Medizinprodukten verwendet werden. Dies hilft den Herstellern, Probleme zu erkennen, die während des Herstellungsprozesses auftreten können. Mit anderen Worten: Immer genau wissen, was, wo und wann.
- Die Einhaltung der FDA- und MDR-Vorschriften ist häufig eine Voraussetzung für den Markteinstieg, nicht nur in den Vereinigten Staaten und der Europäischen Union, sondern auch in vielen anderen Ländern der Welt. Da MedTech-Hersteller weltweit tätig sind, müssen sie diese Vorschriften einhalten und benötigen einen Lieferanten, der ihnen bei der Navigation durch die Vorschriftenlandschaft helfen kann, anstatt nur Geräte losgelöst vom Gesamtprozess zu verkaufen.
Ecoclean hat ein Passivierungsverfahren mit der Bezeichnung Pulsated Pressure Passivation (PPP) entwickelt, das speziell auf die Bedürfnisse der Medizintechnik zugeschnitten ist. Wie funktioniert es und was sind die Vorteile für MedTech-Hersteller?
In der industriellen Teilereinigung arbeiten wir bereits mit einem Verfahren namens PPC (Pulsated Pressure Cleaning). Dabei wird der Druck in der Prozesskammer, die mit dem Reinigungsmedium gefüllt ist, verringert und erhöht, um die zu reinigenden oder zu spülenden Bereiche zu erreichen. Die Luftkontraktion wird genutzt, sobald die Kammer belüftet ist. Unsere Erfahrung mit diesem Verfahren haben wir genutzt, um eine Technologie für Passivierungsprozesse in der Medizintechnik anzubieten, die wir PPP (Pulsated Pressure Passivation) nennen. Diese ermöglicht es, die Oberfläche unabhängig von der Geometrie des Bauteils mit einer Schutzschicht zu versehen, da die Druckveränderung in der Prozesskammer dazu führt, dass die Passivierung chemisch in alle Hohlräume und Löcher fließt.
Das neue Passivierungsverfahren der SBS Ecoclean Gruppe ist ein Quantensprung für die Medizin- und High-End-Technologie.
Herkömmliche atmosphärische Verfahren reinigen und passivieren nur die äußere Geometrie der Teile.
Mit dem neuen Verfahren sind wir in der Lage, Implantate und Instrumente auch in Kapillaren, Innengeometrien und Blindbohrungen zu reinigen und zu passivieren.Gerne laden wir Sie in unser Anwendungslabor ein, um Ihnen dieses bahnbrechende Verfahren zu demonstrieren.
PPC und PPP sind exklusive Reinigungs- und Passivierungsverfahren, die von Ecoclean entwickelt wurden!
In unserem Kompetenzzentrum in Monschau haben wir ein Testzentrum für Feinstreinigung. Was bieten wir dort an?
Ecoclean verfügt in Monschau (Deutschland) über ein voll ausgestattetes Technologiezentrum mit Reinraumlabor und validiertem Reinraum für die System- und Prozessentwicklung. Diese Einrichtung ermöglicht es uns, präzise maßgeschneiderte Lösungen für verschiedene Anwendungen in der Medizintechnik zu entwickeln. Darüber hinaus können unsere Lösungen leicht dupliziert werden, um sie an mehreren Produktionsstandorten zu implementieren.
Das Test Center bietet eine Reihe von Lösungen für die Reinigung und Verpackung von medizinischen Implantaten und Instrumenten. Hersteller finden hier unser gesamtes Portfolio, von lösemittel- und wasserbasierten Einkammersystemen bis hin zu mehrstufigen Ultraschallreinigungsanlagen. Mit dieser Infrastruktur können wir den besten Prozess für die Bedürfnisse der MedTech-Industrie evaluieren. Es ist wichtig, daran zu denken, dass eine der größten Herausforderungen für Hersteller von MedTech-Komponenten darin besteht, mit dem sich ständig ändernden regulatorischen Umfeld Schritt zu halten. Hier kommt die SBS Ecoclean Gruppe ins Spiel und bietet nicht nur die Technologie unserer Teilereinigungs-, Passivierungs- und Sterilverpackungssysteme, sondern auch qualifizierte Unterstützung bei der Erfüllung der Anforderungen und einen Rekalibrierservice, um die Produktion auf dem neuesten Stand zu halten. Und natürlich immer unter Einhaltung der neuesten MDR- und FDA-Vorschriften.
Welche Teilereinigungsanlage von Ecoclean für die MedTech-Industrie vereint innovative Technologie, Nachhaltigkeit und Präzision?
Ecoclean und UCM AG arbeiten gemeinsam an fortschrittlichen Reinigungssystemen für medizinische Geräte, insbesondere im Bereich der Endoskopie. Das Ergebnis dieser Zusammenarbeit ist die UCMPerformanceLine, ein Ultraschall-Tauchreinigungssystem mit mehreren Kammern, das die hohen Sauberkeitsanforderungen für optische Linsensysteme in medizinischen Endoskopen erfüllt. Die UCMPerformanceLine wurde für die effiziente und präzise Reinigung kleiner, empfindlicher Teile wie beschichteter Linsensysteme entwickelt und stellt sicher, dass diese den strengen Sauberkeitsspezifikationen entsprechen. Das System verfügt über ein modulares Design für maßgeschneiderte Reinigung.
Was haben wir sonst noch in unserem Portfolio an Reinigungssystemen für die Medizintechnik?
Wir kombinieren die Technologien von Ecoclean und UCM AG, um Lösungen von A bis Z anbieten zu können, je nach Kundenanforderung und nach entsprechenden Versuchen in unseren Testzentren auf der ganzen Welt. Für die Vorreinigung von MedTech-Teilen und Komponenten verfügen wir über wässrige oder lösemittelbasierte Kammeranlagen wie die EcoCwave oder die EcoCore. Für die Teilereinigung nach der Endbearbeitung bieten wir die UCM-Inline-Tauchanlagen an und schließlich für die Endreinigung und/oder Passivierung unter anderem die UCMPerformanceLine. Für sehr kleine und komplexe Teile haben wir z.B. die UCMIndexLine - kurzum: Wir haben das richtige System für die gewünschte Anwendung.
Welche Technologien zeichnen die MedTech-Lösungen von Ecoclean aus?
Ecoclean unterscheidet sich von anderen Anbietern durch den Einsatz spezieller Software für medizinische Geräte, RFID-Technologie und akribische Prüfprotokolle. Diese Technologien stellen sicher, dass alle Anforderungen an die Identifizierung, Dokumentation und Rückverfolgbarkeit von Komponenten nicht nur erfüllt, sondern übertroffen werden. Unser Expertenteam bietet umfassende Unterstützung während des gesamten Qualifizierungsprozesses, einschließlich IQ (Installation Qualification), OQ (Operational Qualification) und PQ (Performance Qualification) auf Anfrage. Wir wissen, wie wichtig die Einhaltung von Vorschriften ist, und begleiten unsere Kunden bei jedem Schritt des Prozesses.
Contact
Phone: +49 (0)2472 83-0
Email: testcenter.monschau(at)ecoclean-group.net